The full melting of the filler results in a dense layer with optimum adhesion to the substrate. The most common software is for the wear protection, e.g. of tools, but additionally corrosion protection or high temperature resistance could be particularly improved. Common exhausting alloys based on cobalt, nickel and iron are used with and without the addition of onerous supplies. But also specifically tailored materials can be utilized.
Enhance the curb attraction of your home with B&Q cladding. All of our timber is responsibly sourced forest friendly timber.
Cladding gear is usually designed to go well with a specific product or a group of merchandise; this notably applies to the units required for uncoiling of the strip and the feeding tool. The materials and surface of the rolls in addition to their geometrical form (cylindrical or topped) are crucial.
For the same exterior loading, the stress produced in the cladding, both external from the coolant or inside from fission-product swelling of the gas, is decreased in proportion to the wall thickness. However, thick cladding is detrimental to neutron economic system, will increase the amount of the reactor core, raises gas temperature, and costs greater than thin-walled tubing.
In our cladding options we consider the styling and hues, alternative of materials, lighting design and total setting of the constructing as key CI parts, so that every thing matches your particular person requirements. Although the thermal properties of façade coverings was of main importance, right now company identity (CI) aspects are essential to the design of the panels. ACM (aluminium composite), glass, pure stone and sheet metal are just a number of the materials that can be utilized in the wide range of plate-holders and sections. , the place T is absolutely the temperature and β is the burnup.
As the oxide layer grows, the compressive stress on the outer layer of oxide isn't sustained and consequently the tetragonal phase turns into unstable and transforms into the monoclinic section. Such a transformation causes the formation of a fantastic interconnected porosity in the oxide film which allows the oxidizing water to come in touch with the metallic floor. With the event of an equilibrium pore and crack structure within the oxide layer, the oxidation fee successfully turns into linear, a characteristic function of the submit-transition oxidation behavior.
Cladding permits the bulk of the half to be made with inexpensive materials, while providing the surface with desirable properties associated with the more expensive cladding material. Laser cladding has resulted in surfaces with superb end, good homogeneity, and really low porosity. Common materials used for cladding include carbides, iron-based alloys, nickel base alloys, and cobalt base alloys. Laser cladding is a process in which a metal coating is applied onto the surface of an element using a laser as the heat source.
The helium filling gasoline can also be a fairly good conductor, but only so long as it stays uncontaminated by fission products. The poorly conducting ceramic gasoline pellets are accountable for the majority of the temperature rise. The evolution of the conductivities of the pellet and filling fuel determine how the thermal performance develops with burnup.
The ensuing cladding layer was well bonded, and the blades exhibited improved fatigue traits in contrast with blades fashioned by the conventional silver brazing course of. laser beam. The alloy was overlaid on the steel as a powder layer 2.5 mm thick. After melting and bonding by the laser, the alloy layer was 1.5 mm thick and had little or no dilution from the steel. The resulting surface had wonderful wear resistance.

metal v —
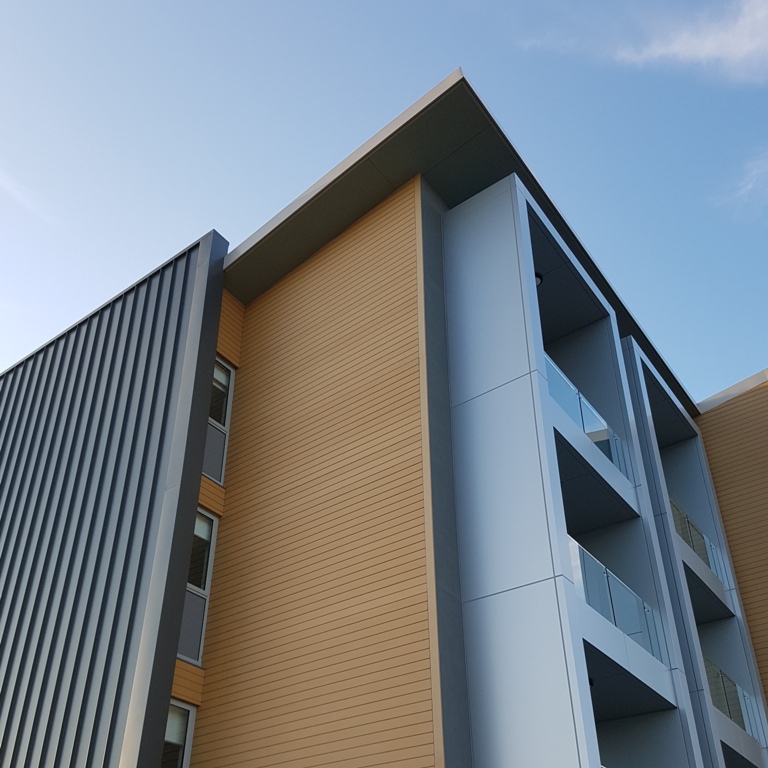
Cladding tools is generally designed to swimsuit a selected product or a gaggle of products; this notably applies to the items required for uncoiling of the strip and the feeding device. The material and floor of the rolls in addition to their geometrical shape (cylindrical or topped) are essential.
In addition to metallurgical factors, water chemistry has a robust affect on the corrosion process in zirconium alloys. The management of water chemistry as required in different reactor methods include appropriate additions of lithium hydroxide, boric acid, hydrogen/deuterium, oxygen, iron, and zinc. In PWRs, boric acid is added to the coolant water for reactivity control. The pH of the coolant is adjusted by addition of lithium hydroxide which renders the coolant slightly alkaline, in order to reduce the corrosion charges of structural materials (stainless steels and Inconels) within the main heat transport circuit and thereby inhibit deposition of corrosion products on the fuel cladding. Radiolysis of water produces oxidizing species which enhances oxidation price of zirconium alloys in the radiation environment .
In our cladding solutions we consider the styling and colors, choice of materials, lighting design and total setting of the constructing as key CI elements, in order that every thing matches your particular person necessities. Although the thermal properties of façade coverings was of major importance, at present company identification (CI) aspects are essential to the design of the panels. ACM (aluminium composite), glass, natural stone and sheet metal are just a number of the materials that can be utilized in the big variety of plate-holders and sections. , where T is absolutely the temperature and β is the burnup.
The helium filling fuel is also a fairly good conductor, but only so long as it stays uncontaminated by fission products. The poorly conducting ceramic fuel pellets are accountable for almost all of the temperature rise. The evolution of the conductivities of the pellet and filling gas determine how the thermal efficiency develops with burnup.
The soften layer is quite skinny; for instance, when cladding an aluminum alloy it's about 0.5–4μm (Kreye 1985, 1997 ). The dilution of the molten zones results in airplane or corrugated interfaces. During mechanical decladding, the fuel assemblies are chopped and the fuel core is leached with nitric acid, forsaking the undissolved cladding material for disposal as a solid waste.
Cladding permits the majority of the half to be made with cheap material, whereas offering the surface with desirable properties associated with the costlier cladding materials. Laser cladding has resulted in surfaces with excellent finish, good homogeneity, and really low porosity. Common materials used for cladding include carbides, iron-based mostly alloys, nickel base alloys, and cobalt base alloys. Laser cladding is a process in which a steel coating is applied onto the surface of an element utilizing a laser as the warmth supply.
Products & Services
Zry manufacturing methods now provide much better management of gaseous impurities than early fabrication expertise, so the unique purpose for adding tin is moot. Since tin is a substitutional impurity, its perform is to extend the energy of Zry over that of pure zirconium. 1.5% tin, and the stability being iron, nickel, and chromium.
Cladding equipment is mostly designed to go well with a specific product or a gaggle of merchandise; this notably applies to the units required for uncoiling of the strip and the feeding tool. The material and surface of the rolls in addition to their geometrical shape (cylindrical or crowned) are very important.
Hydrogen addition in boiling water circumstances is not very efficient because of the segregation of hydrogen in the steam phase. The interplay that gasoline cladding tubes experience because of the fission merchandise on the inside floor is stress corrosion cracking (SCC). Iodine, caesium, and cadmium are a few of the fission merchandise which contribute strongly to the SCC process. Due to the combined effects of thermal expansion of gasoline pellets, gas swelling because of fission gas launch, and the coolant strain on the outer floor of gasoline tubes, cladding tubes collapse on the fuel pellets.
These approaches have encountered issues, including porosity of the cladding, uneven cladding thickness, dilution of the cladding alloy due to the big heat input required, and distortion of the workpiece by the high heat input. Laser cladding has lowered these issues and produced cladding layers with good uniformity, good dimensional management, and minimal dilution of the cladding alloy. provides a survey of a cladding tools. If the incoming strips need to be heated in order to decrease the energy of materials, this needs to be done as shut as potential to the rolling hole and in a protecting environment so as to keep away from oxidation of the cleaned and roughened surfaces. We provide high-quality decorative products that enhance any house and interior.
The constants a and b are basic properties of the fabric and can be decided from commonplace laboratory experiments on fresh fuel. In explosive welding, a compression pressure created by detonation of explosives is used to join overlapping metallic sheets. The joining parts are organized in the direction of one another at an angle of 1–15°, relying on the material and technique, and are prepared with a layer of explosive on the highest. After ignition the joining areas are moved in opposition to one another at high velocity.
laser. The clad substrates confirmed improved oxidation traits compared with the original alloy. Conventional strategies for cladding have employed tungsten-inert gasoline welding, plasma spraying, and flame spraying.

Nuclear Applications: Zirconium browse around these guys Alloys

Zry manufacturing strategies now offer far better control of gaseous impurities than early fabrication expertise, so the unique cause for adding tin is moot. Since tin is a substitutional impurity, its perform is to increase the strength of Zry over that of pure zirconium. 1.5% tin, and the balance being iron, nickel, and chromium.
As the oxide layer grows, the compressive stress on the outer layer of oxide is not sustained and consequently the tetragonal section turns into unstable and transforms into the monoclinic section. Such a transformation causes the formation of a fantastic interconnected porosity within the oxide film which permits the oxidizing water to come back in touch with the metal surface. With the event of an equilibrium pore and crack construction within the oxide layer, the oxidation rate effectively becomes linear, a characteristic function of the submit-transition oxidation behavior.
The soften layer is kind of thin; for instance, when cladding an aluminum alloy it's about zero.5–4μm (Kreye 1985, 1997 ). The dilution of the molten zones leads to airplane or corrugated interfaces. During mechanical decladding, the gas assemblies are chopped and the gas core is leached with nitric acid, abandoning the undissolved cladding materials for disposal as a stable waste.
Zircaloys additionally undergo from bad creep rates. In contrast to floor-layer welding, explosive welding causes no change in microstructure, and corrosion resistance of the layers just isn't affected (Pocalco 1987 ).
Hydrogen addition in boiling water situations just isn't very efficient due to the segregation of hydrogen in the steam phase. The interplay that gas cladding tubes expertise because of the fission merchandise on the inside floor is stress corrosion cracking (SCC). Iodine, caesium, and cadmium are some of the fission merchandise which contribute strongly to the SCC course of. Due to the combined effects of thermal expansion of fuel pellets, gas swelling due to fission gas release, and the coolant stress on the outer floor of gas tubes, cladding tubes collapse on the fuel pellets.
is produced and the risk of a massive secondary hydriding failure is increased. In response to this unforeseen consequence, a number of fixes have been launched.
Joining occurs continuously by native plastic deformation of the contact area (Ruge 1993 ) (see Fig. 1 ). Figure 6 . Schematic diagram showing the mechanism of the oxidation course of and the oxide film construction on zircaloy. Figure 5 .
The complete melting of the filler ends in a dense layer with optimum adhesion to the substrate. The most typical software is for the damage safety, e.g. of tools, but in addition corrosion safety or excessive temperature resistance may be specifically improved. Common onerous alloys based on cobalt, nickel and iron are used with and without the addition of onerous supplies. But additionally particularly tailored materials can be utilized.
Our huge vary of products includes PVC wall panels, outdoors wall cladding, waterproof flooring as a substitute for laminate or LVT, water resistant bathe and loo panels and far more. These embody cladding, small steel pins coupled with a ceramic mass, half-pipes and SiC tiles, in addition to varied types of coatings, including thermal spray coatings. Its characteristic characteristic is the sash bar down the middle of the window and black (much like RAL 9005) steel cladding coverings on the window and flashing which matches traditional buildings. The Independent Expert Advisory Panel additionally suggested the division to ascertain a research venture to test and improve the evidence available on the behaviour of a range of non-ACM supplies used in cladding techniques when subjected to fireplace.
Long-time period, in-reactor, oxidation, and hydrogen choose up habits of zircaloy-2 and Zr-2.5Â Nb stress tubes, showing parabolic and then accelerated linear oxidation and hydrogen pickup kinetics in zircaloy-2. A low and uniform rate of corrosion and hydrogen choose up is seen in the in Zr-2.5Â Nb alloy. Differential swelling between cladding, wrapper tube, and spacing system (spacer wire or grids) can induce additional stresses and deformations on these elements and/or generate coolant circulate perturbations in the bundle. These phenomena have been studied and have significantly proven that wires or grid materials should be chosen and specified so as to decrease differential swelling.
In PWRs the closure of the hole between the pellet and the clad takes about one full power yr whereas the gap is maintained for an extended interval in BWRs. Due to the collapsible clad design of PHWRs, contact between the pellet and the clad is established right from the start of the life of the fuel factor. Laser coating or laser cladding can be utilized to locally functionalize metallic components. In this course of, an edge layer of sometimes zero.1 to 2 mm is applied to the part. The coating material employed is either powder or wire, or utilized upfront as a tape.
Dissolved oxygen in PHWR coolant is controlled between 10–50 ppb and it has been observed that corrosion in each zircaloy-2 and Zr-2.5 Nb strain tubes rises to an exceptionally high worth at excessive oxygen concentrations. The BWR coolant normally incorporates a higher stage of oxygen, usually 200–four hundred ppb.